Continuous process
Resin A
Color 1 – Filler 1
CLEAN XPRESS
The purging step
Resin B
Color 2 – Filler 2
STEP 1 (Only blown film)
After finishing production, mix 50% of CLEAN XPRESS with 50% of resin A, and fill the hopper.
STEP 2 (Only blown film)
While continuing blown film extrusion, reduce screw speed and temperatures, keeping the bubble stable.
STEP 3
When low temperatures are reached, continue blown extrusion with 100% CLEAN XPRESS until the previous polymer or colour pigments are dislodged from the extruder.
STEP 4
To improve effectiveness of cleaning,
increase and reduce screw speed during extrusion.
increase and reduce screw speed during extrusion.
STEP 5
If there is a significant difference in viscosity (MFI) between CLEAN XPRESS and the next resin, mix CLEAN XPRESS and the next resin B at 1/1 ratio.
STEP 6
Extrude the blend for some minutes and adapt the temperatures and screw speed to the new resin B.
STEP 7
The cleaning procedure is finished,
the resin B can be added at 100% and production can start.
the resin B can be added at 100% and production can start.
Discontinuous process
Resin A
Color 1 – Filler 1
CLEAN XPRESS
The purging step
Resin B
Color 2 – Filler 2
STEP 1 (Only blown film)
After finishing production, empty the hopper and ill it with 100% CLEAN XPRESS while continuing extrusion.
STEP 2 (Only blown film)
When CLEAN XPRESS comes to the end of the die, reduce the temperature.
STEP 3
At the lowest possible melt temperature, stop extrusion for 5 minutes.
STEP 4
After that, continue extrusion with CLEAN XPRESS until the previous polymer or colour pigments are dislodged from the extruder.
STEP 5
To improve effectiveness of cleaning,
increase and reduce screw speed during extrusion.
increase and reduce screw speed during extrusion.
STEP 6
When the CLEAN XPRESS is extruding clear at the die, adapt temperatures and screw speed to the next resin B.
STEP 7
When temperatures are reached, remove CLEAN XPRESS from the hopper and fill it with the new resin B.
STEP 8
When CLEAN XPRESS has been flushed out, new production can start.
Guideline adapted to your production
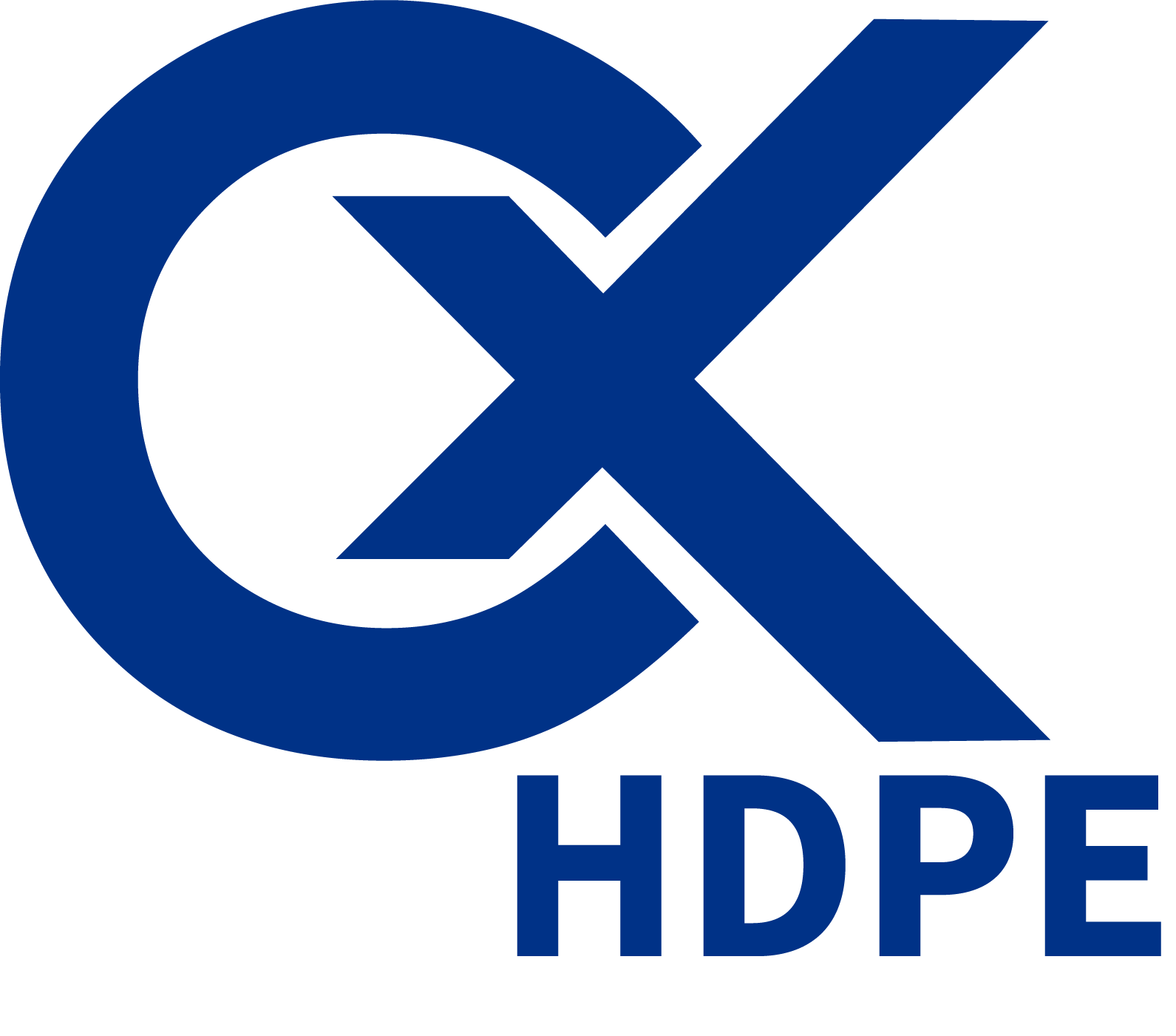
- Blown films
- Cast films
- Wire & cables
…
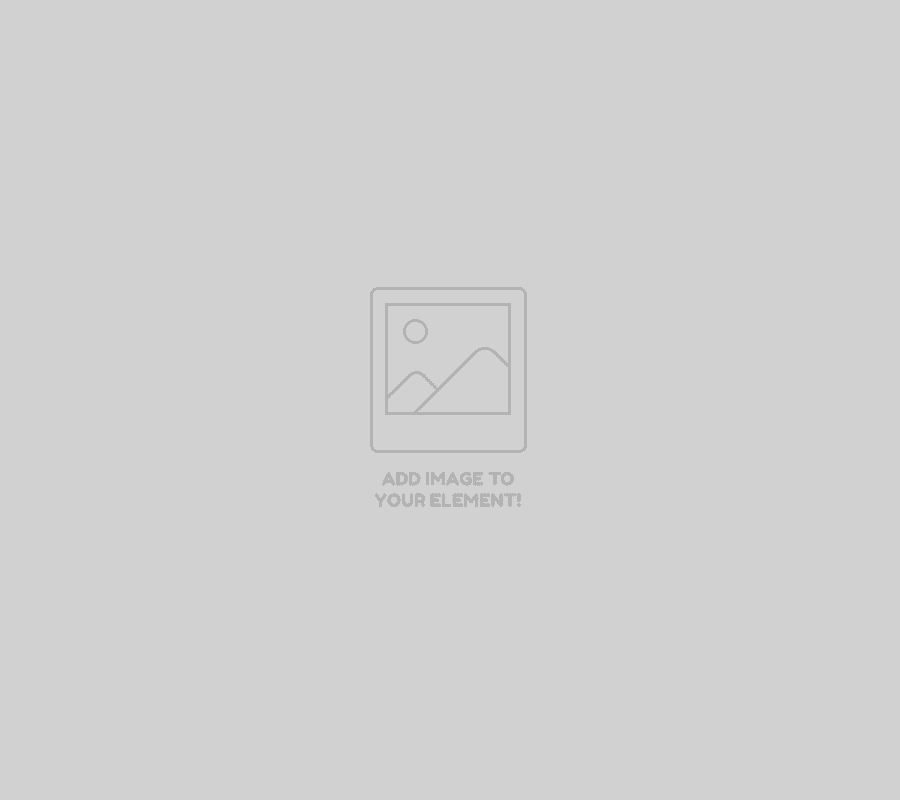
- Blown films
- Cast films
- Barrier films
…
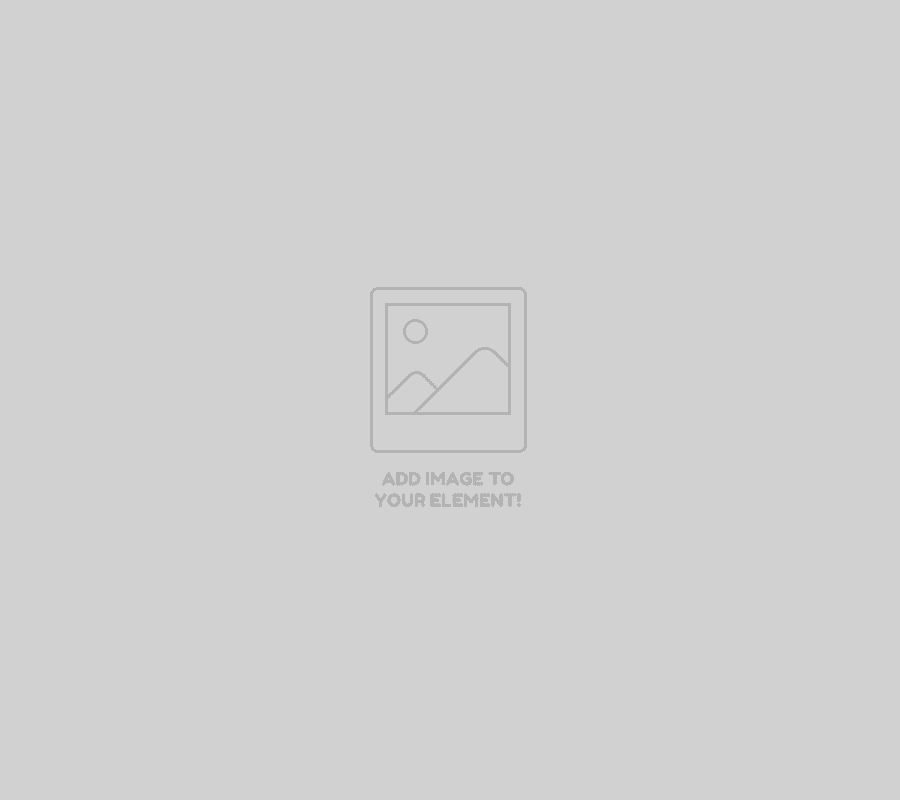
- Blown films
- Barrier film
- Nylon 6, PC
…
- Blown films
- Cast films
- Barrier films
…
- Cast films
- Pipes tubes & profiles
…
- Injection molding with hot runner
…
Compatible with various applications
Blown and
cast films
Wires
& cables
Pipes, tubes
& profiles
Injection
molding
Engineering
polymers
Compounding
More about processes
Please fiil in this short questionnaire, once done, you will receive via email your brochure. All details (MFI, graphic, real case exemple…) are in the documentation. Do not hesitate to download it for free !